「インダストリー4.0」はスマート工場ではない
プレジデントオンライン / 2019年8月5日 6時15分
■スマート工場は「生産」という部分にすぎない
ドイツ政府が2011年に発表し、国家戦略プロジェクトとして推進している「インダストリー4.0」が日本でも注目され、とくに製造業を中心に2015年から17年にかけて一大ブームを巻き起こしたことは、ご記憶の方も多いだろう。だが残念ながら、日本国内では「インダストリー4.0の本質は何なのか? 何が本当の脅威なのか?」について、正鵠(せいこく)を射た議論はほとんど行われていない。
インダストリー4.0に関して、日本のマスコミでは“木を見て森を見ず”な論評が飛び交ったうえ、流行に飛びつきがちな日本市場の特性もあいまって、とくに2016~17年は、製造業で「スマート工場」が大いにもてはやされた。「IoTを取り入れて工場の生産性の向上を図ることが、インダストリー4.0である」と曲解されてしまったわけだ。
だが、本稿で解説するとおり、インダストリー4.0が視野に入れているのは「第4次産業革命」であり、デジタルの力を利用して企業内の業務プロセスや企業間をシームレスにつなぎ(フィジカルなギャップを埋め)、全体最適を実現すること、である。これは製造業と非製造業を問わない。
いっぽうスマート工場は「生産」という一プロセスの中のカイゼンにすぎず、それだけに注力することはむしろインダストリー4.0が目指す全体最適とは対極にあると言ってよい。
■「働き方改革」に踊らされている場合ではない
欧米企業の多くは、90年代~00年代に業務プロセスのERP(基幹業務システム)化、すなわち「インダストリー3.0」への移行を完了した上で、さらにインダストリー4.0に対応してビジネスモデルをバージョンアップしつつある。いっぽう日本企業の現状はといえば、グローバルに事業展開している大手企業でさえ、実質的に「インダストリー2.5」のレベルに留まっているケースも少なくない。
もはや日本人社員の強い現場力に頼るのも限界に達しつつある。いまこそ日本企業をリードするあなたは、「働き方改革」といった実体のないキーワードに踊るのでなく、現実を見据えた施策に踏み出す必要がある。
■「つながること」の先を見ている
ヘニング・カガーマン博士。2009年から9年間にわたってドイツ工学アカデミーの会長を務め、インダストリー4.0の生みの親と称される。2018年8月、SAPジャパンの招聘に応じて来日したカガーマン博士は、講演の中で以下のように述べた。
●インダストリー4.0はまず13年にドイツの主要産業である製造業から着手したが、その後15年には対象をサービス業に広げ、さらに17年には「社会全体の自律化」へ、と着実に当初のビジョンを実現しつつある
●日本と同様、ドイツ製造業も、経験の長い熟練工の“匠の技”を差別化要因としてきたが、そこにデジタルの力を加えることで、単なる「モノづくり」でなく、モノが発揮する機能を売る「コトづくり」に視線をシフトしてきた
●「つながること(Connected)」それ自体は3.0の時代からあるもので、それだけでは4.0が目指す全体最適にはつながらない。可視化、透明性、予測可能性、自律化、へと発展していくことが目的である
■単なる「スマート工場」「IoTやAIの導入」という誤解
いっぽう日本政府も、ドイツの動きに呼応するように、16年4月には「ソサエティ5.0」を発表。工業社会(3.0)、情報社会(4.0)に続く「超スマート社会」(5.0)を目指す、と打ち上げた。さらに17年3月からは、ソサエティ5.0を実現するための実行施策として「コネクテッド・インダストリーズ」を推進している。
どちらも、「デジタルの力」を取り込むことで、フィジカル世界のギャップを埋め、企業や社会の生産性と競争力を引き上げていこうという基本方針である。
ところがいっぽうで、とくに国内製造業の一部には、インダストリー4.0を単なる「スマート工場」あるいは「生産工程へのIoTやAIの導入」と狭く捉えてしまい、むしろインダストリー4.0が目指す「全体最適」のコンセプトには逆行する方向への動きもある。具体的に見てみよう。
図表1を見ていただきたい。「製造業」の生産プロセスをごく単純化した図だ。真ん中に「工場(生産)」があり、左にその「前工程」、右に「後工程」を置いている。
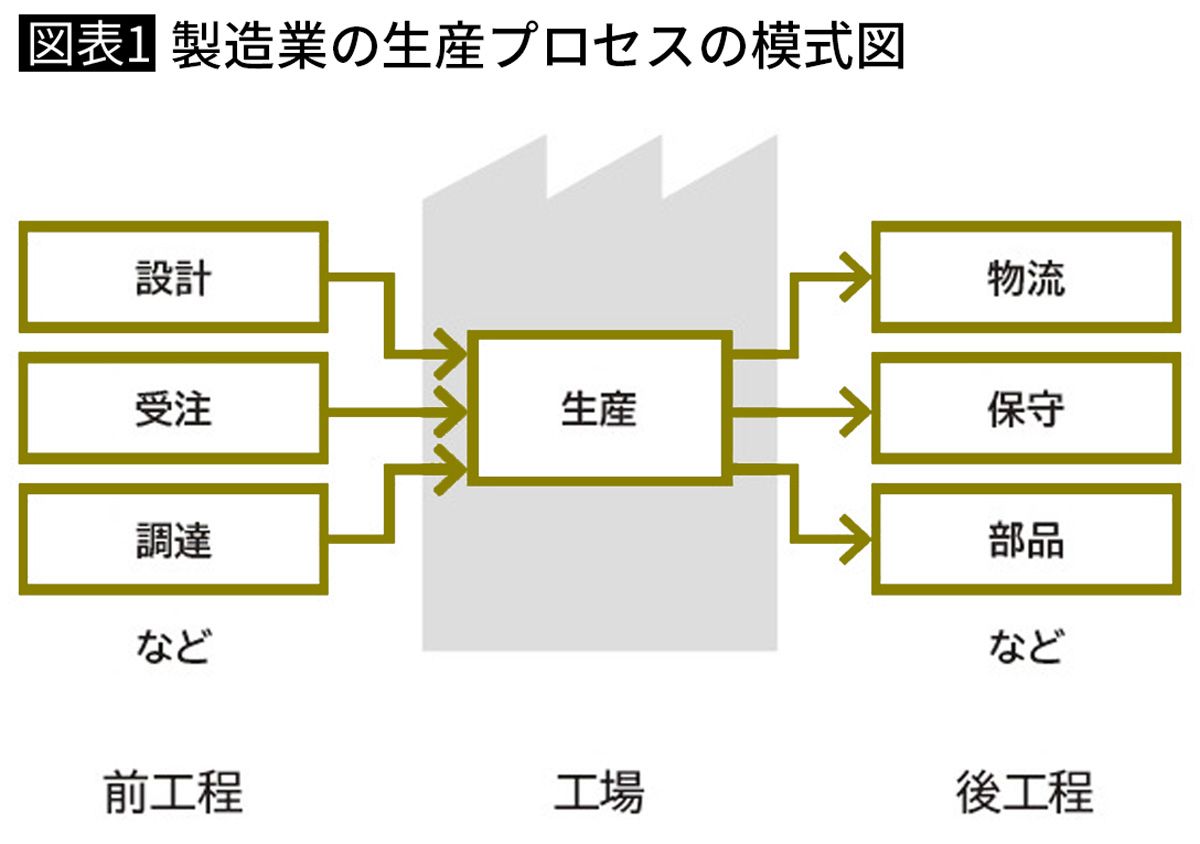
前工程はおもに「設計」「受注」「調達」の3系統がある。工場は研究開発部門が「設計」した図面を受け取って製品の生産を開始する。生産数量は営業部門が顧客から取ってくる「受注」の数に合わせるし、適切な部材や原料が揃っていなくては作れないから「調達」の工程もある。この3つの前工程の後に、工場での「生産」が行われる。
いっぽう後工程には「物流」「保守」「部品」などがある。製品のカテゴリーによっても大きく異なるが、生産された製品は、「物流」のプロセスによって顧客または代理店、販売店などに運ばれていく。製品寿命が長いものなど、「保守」のプロセスが製品の品質そのものと同じくらい重要なカテゴリーも多く、また「部品」の管理と、注文に応じた部品の供給も重要であることが多い。
■「カイゼン文化」が曲解の最大の原因
この中で、日本の製造業が圧倒的な強みを持つのが、中央の「生産」の工程、つまり「工場の現場」だ。
日本の製造業の生産技術を世界最高峰に押し上げた原動力が、生産現場におけるカイゼン活動であることは論を俟たない。きわめて勤勉で優秀かつ勤続年数が長い現場のワーカーが、日々発見する不都合をその都度「カイゼン」し続けることで、世界に類を見ない最高品質の生産現場を作り上げた。
実際、工場の現場を歩くと、現場社員による業務改善の積み重ねには圧倒される。脈々と積み重ねられた経験値が方法論化され、基本として実践されるいっぽうで、さらなる創意工夫が日々追加されている。カイゼンは海を越え、世界にも広がっている。「トヨタ生産方式」は自動車業界のみならず、世界のあらゆる製造業、最近では非製造業までが参考として取り入れている。
ところが、この最強を誇った「カイゼン文化」こそが、インダストリー4.0を曲解してしまった、
最大の原因でもあるのだ。それはなぜだろうか?
■日本の工場はすでに世界最高水準の生産性
インダストリー4.0を「IoTという新たな技術を用いたカイゼン」と捉えた日本の製造業の一部は、さっそくインダストリー4.0の取り入れ方を考え始めた。その結果として起こったのが「スマート工場」ブームだ。
たとえば、工場に並ぶ製造装置にセンサーを取り付けて、異音や振動、温度上昇などをモニタリングし、いち早く異常を検知して故障の予防につなげる、といった活動だ。
だが、日本の工場の中は、すでに世界最高水準の生産性だ。カイゼンの余地、すなわち生産性の向上の“伸びしろ”がどのくらい残っているのだろう?(図表2)
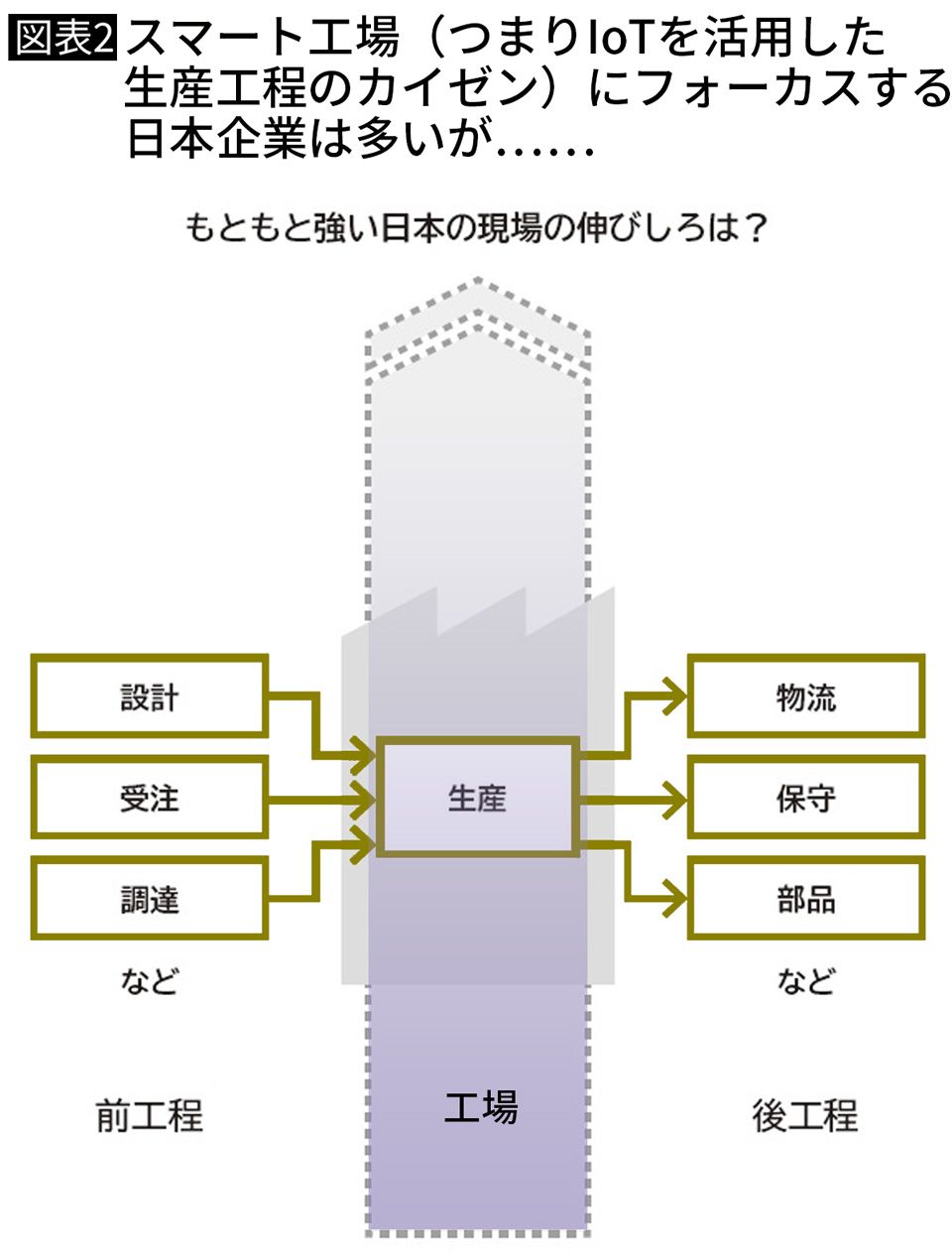
製造現場に関わる方々は、口を揃えて「いやいや、まだまだ改善の余地はあります」と本心から言う。それは実際、その通りなのだろう。しかし、世界的な視野で見れば、国内の工場の生産品質は頭抜けている。逆にいうと、IoTを取り入れた、工場内のカイゼン活動による伸びしろは、相対的には限られる。
■ドイツ勢が製造業競争の「土俵」を変えつつある
いっぽう、その「世界最高の現場力」にチャレンジし続けながら、ついに勝てなかったのが、ドイツ勢だ。日本と肩を並べる高品質の製品で知られるドイツの製造業であるが、こと工場内では、日本のカイゼンにはかなわなかった。製品の品質ではやはり日本製が一番、ということも多かったのである。内心、ほぞを噛んでいたに違いない。
ところが、デジタル・イノベーション時代の到来をうけ、ドイツ勢は気づいたのだ。
日本の製造業は、「生産」の工程、つまり「工場の中」ならダントツだ。しかしいっぽうで、「工場の前・後」、つまり「前工程」や「後工程」は、業務生産性は必ずしも高くないし、前後の連携もよくない。それぞれのプロセスが部門ごとに分かれており、個別最適が進むいっぽうで全体最適が図られていないため、全体としての生産性には難がある。
ということは(図表3のように)、「工場の中」=製品の品質で勝たなくとも、前工程と後工程も含めた、広い意味での業務品質であれば勝算がある。そこでドイツ勢は、「工場の中」の品質それ自体で勝負するのではなく、「前工程」から「後工程」までを一気通貫につなぎ、エンド・トゥ・エンドのプロセスを「全体としての顧客価値」として提供することで、製造業の競争の土俵を変えようとしているのである。
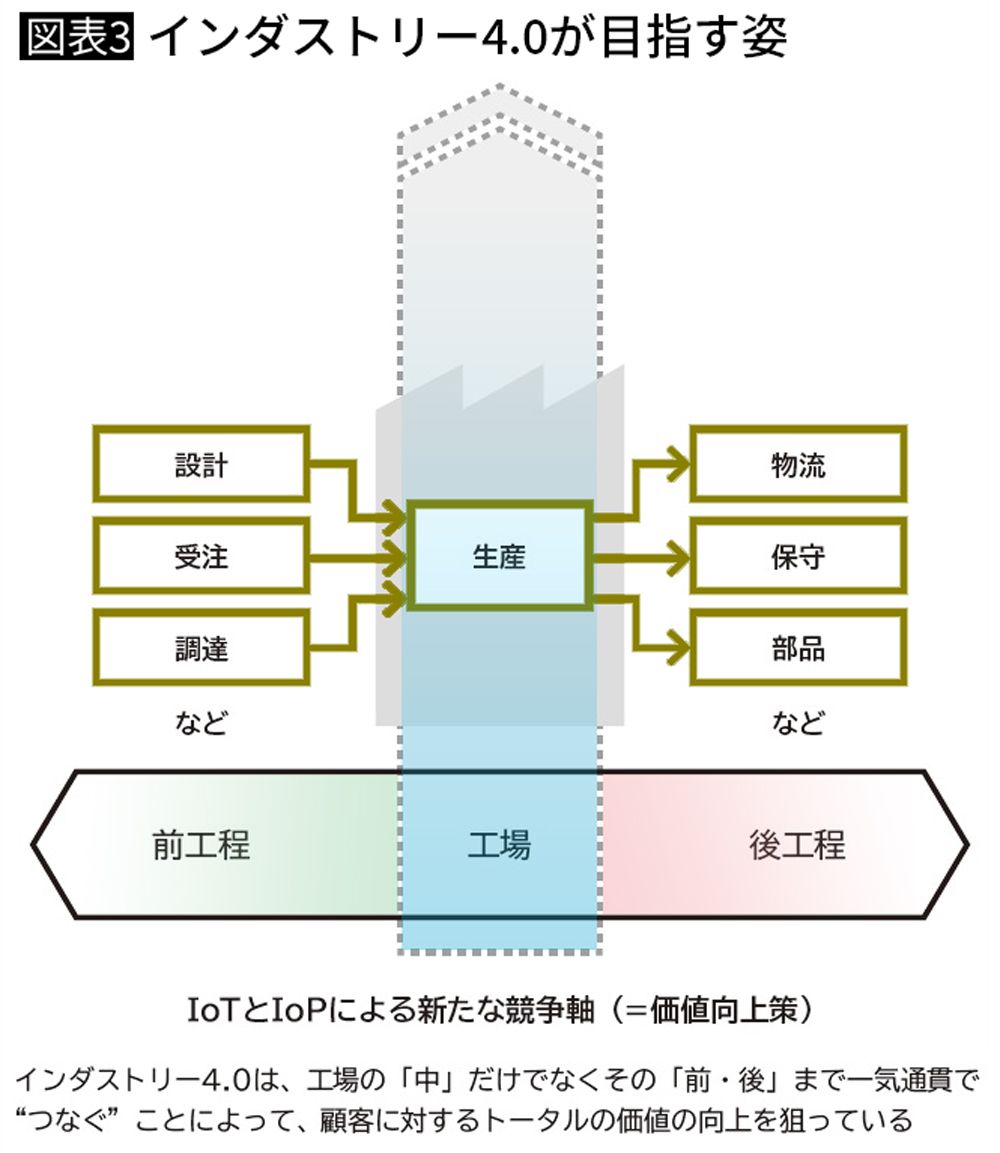
■顧客がほしいのは「10年間メンテ不要」ではない
その典型例が、ケーザー・コンプレッサーである。コンプレッサー業界でも、製品単体での品質でいえば日本製は非常に優れている。メンテナンスをせずとも10年間故障知らず、といったケースもあるそうだ。
だが顧客が望んでいるのは必ずしも「10年間メンテ不要」ではない。「ケーザー側が責任をもって適切にメンテナンスを行ってくれ、その結果10年でも20年でも、圧縮空気が安定的に供給され続ける」のであれば、顧客にとってはむしろその方が望ましいからだ。
そこでケーザーは、コンプレッサー単体の品質に加えて、売り切りでなく従量課金での提供、リモートからの異常検知とタイムリーな保守員の派遣、予測保守による先回りの対応、といった「後工程」のサービスと組み合わせることで、顧客の真の欲求に応えようとしているのだ。
この観点では、日本勢が「スマート工場」にいくら注力しても、それはインダストリー4.0を推進するドイツにとっては、何ら脅威ではない。むしろ日本が旧来得意としている工場内の部分最適の追求、生産工程カイゼンの延長線上の取り組みにすぎないからだ。
■「現場を見ればすべてわかる」という落とし穴
ちなみに、「インダストリー4.0先進工場」をドイツに視察に行った日本企業の生産技術のベテランが、「うーん、意外に大したことないね」といった印象を持って帰ってくることがよくある。「ウチのほうが進んでいるんじゃないか?」くらいのことを言うこともある。
日本の生産技術は、過去50年以上にわたって現場のカイゼンに取り組み、結果、世界最高水準の現場の生産品質を作り上げた。彼らこそがまさに、「モノづくりニッポン」を支える、縁の下の力持ちたちだ。
当然、彼らは、「現場を見ればすべてわかる」と強い自信を持っている。それはそうだ。現場を一目見れば改善点がわかってしまう、彼らの経験と見識こそが、世界最高の現場を作ったのだから。
しかしここに大きな落とし穴がある。彼らは、フィジカルなカイゼンしかやったことがないのである。前述のように、インダストリー4.0の狙いは「前工程・工場・後工程をデジタルによって一気通貫につなぐ」ところにある。つまり、インダストリー4.0の本質は「工場を視察」しても見えないのだ。
また、「インダストリー4.0的なことは日本企業でも以前から取り組んでいる」といった意見もある。だが彼らが言う「4.0的な活動」とは、要は「スマート工場を作る」ことなのである。
■「スマート工場」は従来の延長線上にあるだけ
念のため付記しておくと、日本の製造業には2種類ある。製造装置やセンサーなどのメーカー、つまり「スマート工場」を売っている製造業と、それを買って使う立場にあるその他の製造業である。
前者の製造装置やセンサーなどのメーカーが、この「スマート工場」ブームを商機ととらえ、ブームをさらに盛り上げようとするのは、企業活動としては当然である。せっかくの盛り上がりを見逃す手はない。「弊社のスマート工場向け製品を導入すれば、現場のさらなるカイゼンが進みます」との主張で盛り上げをはかるのは当然だ。
しかし後者の、それを「買う」側の企業は、よく注意しなくてはならない。スマート工場を買えば、工場内のカイゼンはさらに一歩進むかもしれないが、それは従来から得意としていたやり方を続ける(タテ軸を伸ばそうとしている)にすぎず、インダストリー4.0つまり第4次産業革命への対応という観点からすればむしろ逆行しているとすら言えるからだ。
■経営者が動かないと「4.0」には近づけない
こうした状況下、では日本勢は、どのように対応したらよいのだろうか。
結論から言えば、これに対応できるのは経営者だけだ。
生産技術部門や工場長は、「生産」の工程にしか権限がない。工場の「前工程」や「後工程」には権限は及ばない。それをやろうとすれば、いわゆる「組織の壁」を越えて前工程や後工程と協力しなくてはならないが、それは過去50年、彼らがあまり得意としていないスキルだ。
しかもインダストリー4.0は文字通り、業務プロセスに「革命的」な変革を起こすことになる。前工程や後工程においても改善レベルでは済まず、これを実行できるのは部門長や部門管掌役員レベルではない。工場内の個別最適ではなく、全社視点での全体最適を実現する、と経営レベルで決断しなければ絶対に対応できない。
経営者がインダストリー4.0を「スマート工場化」とみなし、「工場長や生産技術部長が頑張ればよい活動」と誤解している限り、日本の製造業は4.0には近づかないのである。
■「タテ軸オンリー」か「タテ軸×ヨコ軸」か
もうひとつ念のため付記しておくと、「スマート工場化などのカイゼン」と「インダストリー4.0が目指す全体最適」は、いっぽうが常に優れていて他方は劣っているという話ではまったくない。
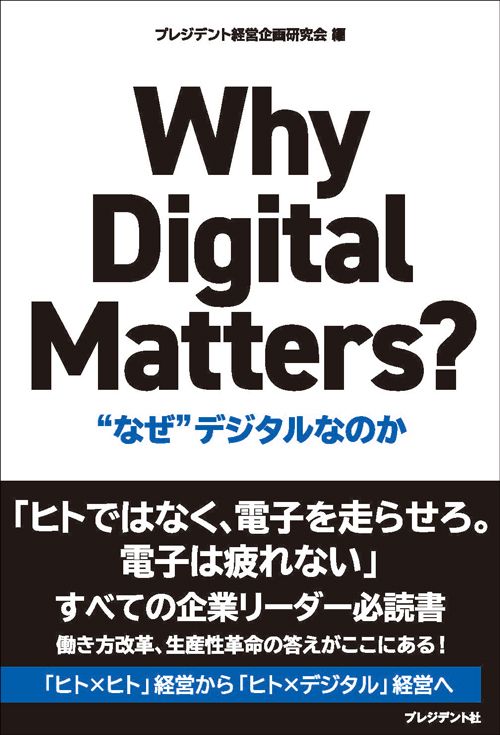
前掲の「図表3 インダストリー4.0が目指す姿」における、タテ軸とヨコ軸のどちらを追求するのが最適かは、企業ごとに違う。ヨコ軸つまりデジタルの力を借りて全体最適を目指すことのハードルは決して低くない。すべての企業が一様に4.0を目指すべきだというものではない。
ただ大切なのは、「タテ軸」と「ヨコ軸」という2つの異なる選択肢があることを理解したうえで、どちらを選択するか、を経営者が真剣に検討することだ。自社が「タテ軸つまり生産現場におけるカイゼンに集中する」か、「タテ軸×ヨコ軸の合わせ技、つまり従来の強みにデジタルの力を掛け合わせて合わせ技で右上を目指す」か、の選択だ。この2つがまったく異なるアプローチであるのはすでにおわかりだろう。
一番悪いのは、インダストリー4.0を過去数十年間ずっとやってきたカイゼンの延長線上にあると勘違いし、カイゼンの継続で4.0に対応しているつもりになってしまうことだ。
----------
SAPジャパン株式会社 IoT/IR4ディレクター
顧客およびパートナーとの共同イノベーション事業開発を担当。海外事例にも精通し、講演・執筆など多数。SAP IoT研究会主宰。米国ライス大学にてMBA取得。
----------
----------
SAPジャパン株式会社 IoT/IR4ディレクター
顧客およびパートナーとの共同イノベーション事業開発を担当。海外事例にも精通し、講演・執筆など多数。SAP IoT研究会主宰。米国ライス大学にてMBA取得。
----------
(SAPジャパン株式会社 IoT/IR4ディレクター 村田 聡一郎 写真=iStock.com)
外部リンク
この記事に関連するニュース
-
富士通CTOが説く「AIエージェントが動かすエンタープライズの将来像」とは
ITmedia エンタープライズ / 2024年9月18日 7時0分
-
エスマット、ICCサミット KYOTO 2024「CATAPULT GRAND PRIX」にて5位入賞
PR TIMES / 2024年9月6日 17時40分
-
製品ライフサイクル全体でのデータ連携で日本製造業における変革のスピードアップに挑む
PR TIMES / 2024年8月27日 12時15分
-
製品ライフサイクル全体でのデータ連携で日本製造業における変革のスピードアップに挑む
@Press / 2024年8月27日 10時0分
-
マクニカ、田中精密工業へ生産シミュレーションソフトウェア「PlantSimulation」を提供
@Press / 2024年8月21日 10時0分
ランキング
-
1お金持ち流!100円ショップで買うもの・買わないもの
オールアバウト / 2024年9月18日 21時40分
-
2ローソン、107円になる「長すぎるパン」を発売 「大きすぎるパン」も KDDIと共同開発した背景
ITmedia ビジネスオンライン / 2024年9月19日 16時44分
-
3マイナ保険証では"大損"する人が続出…廃止される健康保険証だけに記載された最重要情報で医療費は雲泥の差
プレジデントオンライン / 2024年9月19日 10時15分
-
4社長ら報酬返納=再処理工場の完成延期で―日本原燃
時事通信 / 2024年9月19日 19時49分
-
5下請けいじめ、懸念事案あり 日本自動車工業会が緊急点検
共同通信 / 2024年9月19日 13時3分
記事ミッション中・・・
記事にリアクションする

記事ミッション中・・・
記事にリアクションする

エラーが発生しました
ページを再読み込みして
ください
