製造業なのに「モノからコトヘ」と言い始める企業はこれから危ない
プレジデントオンライン / 2020年10月26日 11時15分
■国内拠点に期待される「戦うマザー工場」としての役割
——トヨタの工場では春以降、減産が続いていた時期に工場を挙げて作業者の多能工化、設備製作の内製化など体質強化活動に取り組んだようです。日頃からカイゼン活動しているトヨタだと思いますが、さらに磨きをかけた形です。ウィズコロナ、アフターコロナをにらんで日本のものづくり産業がしなければいけないカイゼン活動とは何でしょうか。
【藤本】今回の新型コロナウイルス感染拡大のように世界のどこの工場が止まるのかわからない「グローバル災害」の場合、各社のグローバル・サプライチェーンの中で、日本の国内工場が最後まで動いている、あるいは災害終息後に最初に立ち上げるのは日本の工場である可能性は小さくありません。加えて、海外拠点にもそうした組織能力を構築する必要があり、国内拠点は自らが存続しつつ、それを知識移転する「戦うマザー工場」としての役割がますます期待されます。
その点、トヨタ自動車は、例えばかつて大きな経済危機に直面したタイやトルコの生産子会社でも、安定雇用をできるだけ維持した上で、余剰労働力を教育、訓練、改善などに回し、現場力を高めることによって、危機後の競争力向上につなげた実績が豊富です。グローバル災害の時代に、競争力と危機対応力の同時構築は、日本だけではなく海外拠点でも必須です。
■日本の優良な工場群の存在感は、コロナ後にむしろ増す
【藤本】日本の国内工場は相対的に高賃金という弱点は依然としてありますが、それを高い生産性、製造品質、即応力などで補った上で、「見える災害」に対する早期復旧と代替生産によるサプライチェーン維持能力と、コロナ禍のような「見えない災害」に対する感染防御力を維持し、かつ海外拠点に伝えることで、国内のものづくり現場は、日本企業のグローバル・サプライチェーンを牽引していくだけの力を持ち続けていると思います。
アフターコロナにおける貿易財製造企業のグローバル・サプライチェーンを再構築する際に、日本の優良な工場群の重要性と存在感は、むしろ増すのではないでしょうか。
——とすればアフターコロナをにらんでも、日本企業のサプライチェーンの見直しは必要ないということですか。
【藤本】必ずしも、恒久的あるいは不可逆的な変更だとは限りません。アフターコロナを考えると、短期的な危機対応の判断によってグローバル・サプライチェーンを変更し、国内完結型に変えるという戦略は、それが国際競争力を損なうのであれば正しくない、ということはすでにご説明しました。
グローバル競争は毎日来るのですから、グルーバル型であれ、ローカル完結型であれ、あくまでも自社の当該製品にとって「競争力ベスト」のサプライチェーンを維持し、その長期的な全体最適を目指すべきだと思います。
■かつて国内工場を全面閉鎖した企業は「流れ」を読み間違えた
【藤本】とはいえ、生産拠点を国際展開している日本の多くのグローバル企業は、国内に加え、中国やASEAN(東南アジア諸国連合)などを含むアジアのサプライチェーンを既に持っているのが一般的です。その日本、中国、ASEANの「三角形」のバランスは、災害危機対応というよりはむしろ、競争力対応という見地から、見直しが必要なケースも増えていると思います。
——どのように見直せばいいのでしょうか。
【藤本】長期的視点が必要なので、日本のグルーバル・サプライチェーンを歴史的に振り返ります。
多くの日本製造企業、特にデジタル化、モジュラー化により「設計の比較優位」を失った家電エレクトロニクス系の企業は、1990年代に圧倒的な低賃金と労働力動員力で世界の工場となった中国において生産拠点を急増させました。
この時、日本の国内マザー工場を閉鎖し、中国など低賃金国に生産拠点を全面的に移した企業もありました。しかし、短期的な原価計算だけで国内工場を全面閉鎖してしまった企業の本社は、いずれ中国の賃金も上昇に転じるという国際経済の大きな流れをちゃんと読めていなかったようです。
■中国拠点の縮小はないが、ASEAN拠点の拡大はあり得る
そのような企業は、海外拠点の生産性向上を支援する国内マザー工場がもはや無いため、中国が賃金高騰の時代に入ると、中国拠点自体がコスト的に厳しくなり、低賃金を求めてベトナムやインドネシアなどさらに低賃金の国へ標準品の量産拠点を移すしかありませんでした。生産性向上の組織能力が乏しく、低賃金頼みのグローバル・サプライチェーンは、競争力的にだんだん行き詰まってきます。これに気が付き、国内のマザー工場を再構築して「三角形」のバランスを回復させた日本企業も実際に存在します。
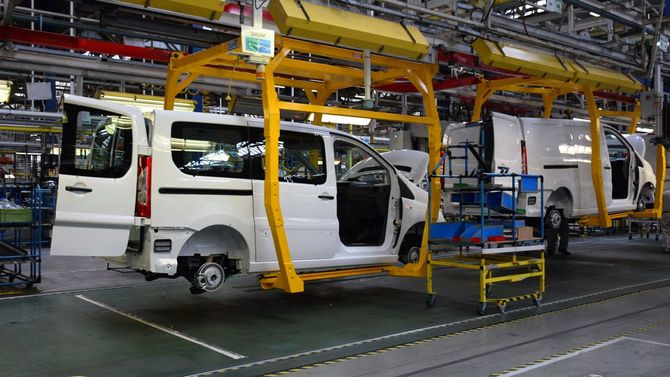
このように、2005年ごろから中国の賃金が高騰し始め、中国工場のコスト競争力は低下し始めました。しかしいったん中国につくった多数の工場は、中国政府との関係もあり、中国工場自体の頑張りもあり、あるいは簡単には撤退しない日本企業の方針もあり、多くが存続しています。
さらに、中国の市場自体が巨大化してくれば、かつての米国拠点のように、現地市場向け工場としての意味も出てきます。ですから、中国拠点の撤収は、多くの日本企業は考えていないと思います。
とはいえ、1990年代に中国に大挙進出した歴史を踏まえて考えるなら、グローバルな全体最適経営の観点からは、日本企業の中国生産の比率がやや過大となっている可能性はあります。中国拠点を縮小する必要はないかもしれませんが、ASEAN等の非中国拠点をより速く拡大させるという判断はあるかもしれません。
■日本のものづくり現場は小さくなりすぎている可能性がある
【藤本】ASEAN諸国をみると現状ではベトナムなど、中国に比べて低賃金の国が多く、工場の現場力やインフラの水準も徐々に上がっているので、日本企業の量産・輸出拠点として、より好適地となりつつあります。中国企業自体もASEANに生産拠点をシフトしている時代です。
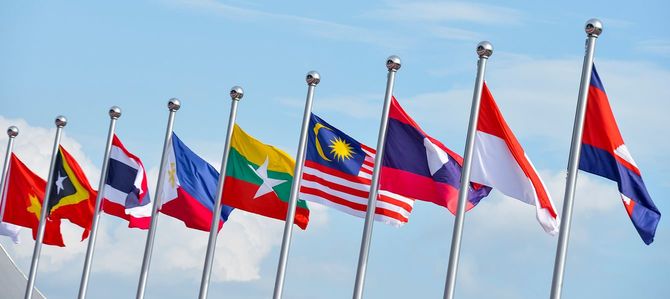
一方、日本のものづくり現場は、企業によっては、過去の短期的な経営判断から、あるべき姿よりも小さくなりすぎている可能性はあります。
むろん日本は人口減少と労働力不足が続きますから、国内量産工場の大建設は多くの場合考えにくいですが、それでも、設計の比較優位や、生産性、付加価値、荷姿などによっては、国内工場が輸出拠点として、今でも拡大しているケースは、電子部品、医療関連製品などの分野で、実際に見られます。要するに、グローバルな日本企業の国際拠点配置は、まさに産業次第、企業次第で異なります。
以上を総合すると、現在の日本企業のグルーバル・サプライチェーンの形は、全体最適の形に比べると相対比において「中国過大、日本過小、ASEAN過小」となっている場合もあるのではないかと考えます。つまりアフターコロナをにらんだ長期的な「競争力ファースト」の戦略として、「国内強化、ASEAN強化」へと修正する企業が少なからずあると考えます。いずれにせよ、グローバル・サプライチェーンの再編成は、あくまでも、短期的な新型コロナ危機対応ではなく、長期的な競争力重視で決めるべきです。
■中国の工場と日本の工場の「進化」は異なってくる
——国内、中国、ASEANの工場はどのような位置づけになるのでしょうか。
【藤本】国内の優良工場は多くの場合、多能工のチームワーク力を蓄積してきた歴史的経緯から、「戦うマザー工場」として、複雑で面倒な擦り合わせ型アーキテクチャの部品や資本財や最終製品を、面倒な「変種変量変流生産」で作ることが得意です。今後、中国企業は遠隔操作でシンプルな製品をシンプルな流れで作る「お手軽な自動化工場」への指向を強めるでしょうから、日本企業とは進化の経路が異なってくると予想します。
一方、日本の優良国内工場は、工場のフロアに作業集団が残り、それをAIやサイバーフィジカルシステムが適宜支援し、ややこしい製品と工程を臨機応変に動かしていく形が、勝ちパターンになっていくと私は予想します。
■中国は「輸出拠点」から「供給拠点」に変わっていく
そうやって、デジタル化、スマート化に流れも取り込みながら、結局は人が残り、日々、カイゼンを進め、組織能力を高めているものづくり現場を国内に確保する。そして、いざという災害時には早期復旧も代替生産もでき、感染防御力も高く、その経験知を中国やASEAN等の海外拠点にも教えることができるという存在になっていくでしょう。
日本企業の海外拠点は、日本拠点ほどではないものの、中国企業などに比べれば、もう少し面倒な擦り合わせ型製品のものづくりに力を入れ、特にASEAN等の海外工場はその有力な輸出拠点として育てていく。一方、賃金が高騰している中国は輸出拠点というよりも中国現地市場への供給拠点としての比重が増すでしょう。
こうして、平時には日本国内、中国、ASEAN等の工場がそれぞれの特長を生かして、製品や企業の特性により、グローバル補完型あるいはローカル完結型のサプライチェーンを築き、全体で国際競争力を高めるという考え方が望ましいと思います。
■伸縮自在な「グローバル・ローカル・サプライチェーン」へ
そして緊急時には「戦うマザー工場」である国内の工場が、中国やASEANの拠点を遠隔通信も含め支援し、被災拠点は速やかに復旧し、必要に応じて互いに代替生産し、グローバル展開サプライチェーンをローカル完結サプライチェーンに、あるいはその逆に、迅速に切り替える「サプライチェーン柔軟性」を持つことが重要です。
要するに、平時がグローバルなら緊急時にはローカルに、平時がローカルなら緊急時はグローバルにと、自在に陣形を変えられる、伸縮自在な「グローバル・ローカル・サプライチェーン」が、アフターコロナ時代のグローバル経営の一つの形でしょう。
そのためには日本国内の工場だけでなく、中国やASEANの工場でも日頃から組織能力を高める努力をしなければならないのは言うまでもありません。その中心に、日本の「戦うマザー工場」が存在しうるわけです。
■「モノを捨ててコトに走る」というのは不毛な二者択一
——なかなか複雑な連立方程式を解くような経営戦略ですね。
【藤本】SNSの時代においては、短くて、格好の良いキャッチコピーのような言葉が、一般にも資本市場にもアピールする傾向があります。しかし、そういう、バラバラの問題にバラバラに答えるタイプの言葉に、経営戦略をゆだねるのは危険かもしれません。
例えば「モノからコトヘ」ということが最近よく言われますが、それをキャッチフレーズに「もうモノは作らない。サービスに特化する」という経営戦略を口にする会社も散見されます。しかし、モノとコトは経済学的には代替関係ではなく補完関係にあるものです。
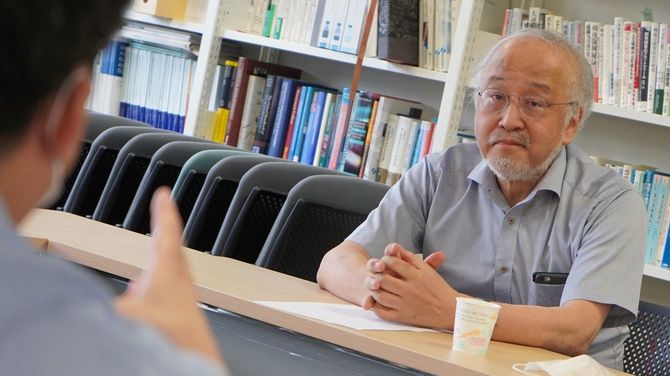
良いモノ(製品)があって、よいコト(サービス)が実現し、良いコトがあるから、良いモノが作れるのです。確かに、モノを売りっぱなしにするビジネスモデルには限界があり、客先に設置された自社のモノからデータを取ってコトにつなげるソリューションビジネスは、日本の多くの物財企業の行くべき道でしょう。
しかしそれは、あくまでも良いものを作ったうえでの話であり、モノを捨ててコトに走るというのは、言葉遊びとしては心地よいが、モノゴトの本質からは外れた、不毛な二者択一に見えます。経営者は、そういうはやり言葉にすぐには飛び付かず、まず連立方程式をじっくり解いてから一言を発する。つまり本質を地道に見極めながらの経営判断を下してもらいたいと思います。
----------
東京大学大学院経済学研究科教授
1955年生まれ。東京大学経済学部卒業。三菱総合研究所を経て、ハーバード大学ビジネススクール博士課程修了(D.B.A)。現在、東京大学大学院経済学研究科教授、東京大学ものづくり経営研究センター長。専攻は、技術管理論・生産管理論。著書に『現場から見上げる企業戦略論』(角川新書)などがある。
----------
----------
Gemba Lab代表、経済ジャーナリスト
1957年生まれ。早稲田大学理工学部卒業、東京工業大学大学院修了。日経ビジネス記者を経て88年朝日新聞社に入社。東京経済部次長を経て、2005年編集委員。17年Gemba Lab株式会社を設立。東洋大学非常勤講師。著書に『これからの優良企業』(PHP研究所)などがある。
----------
(東京大学大学院経済学研究科教授 藤本 隆宏、Gemba Lab代表、経済ジャーナリスト 安井 孝之 聞き手・構成=安井孝之)
外部リンク
この記事に関連するニュース
-
大河原克行のNewsInsight 第309回 どうなる日立エアコン、「白くまくん」シリーズの今後
マイナビニュース / 2024年7月27日 23時4分
-
2025年以降の投資促進に向け、ASEAN事務局が各国ビジネス協議会と議論(ASEAN、タイ)
ジェトロ・ビジネス短信 / 2024年7月25日 1時25分
-
アジア各国のホワイトカラー人材紹介市場の動向 2024年4月~6月
PR TIMES / 2024年7月17日 18時15分
-
第3回タイ・EU FTA交渉と第7回ACFTA 3.0交渉実施(ASEAN、タイ、EU、中国)
ジェトロ・ビジネス短信 / 2024年7月16日 0時25分
-
サプライチェーンが持つ脆弱性の打開のカギは企業幹部の「インセンティブ改革」にあり
ニューズウィーク日本版 / 2024年7月3日 15時56分
ランキング
-
1芦別岳の旧登山道近くで倒れている男性発見 その後死亡確認 札幌市の77歳男性が遭難した可能性 北海道・芦別岳
北海道放送 / 2024年8月1日 22時13分
-
2紅麹サプリと同等量使用、新たに4社8製品 2製品には「プベルル酸」 再調査で報告漏れ
産経ニュース / 2024年8月1日 21時5分
-
3兵庫知事側近の総務部長が病欠 パワハラ疑惑に対応 離脱幹部3人に
毎日新聞 / 2024年8月1日 20時21分
-
4「不誠実だった」 NUMOが北海道・寿都町民に陳謝 文献調査巡り
毎日新聞 / 2024年8月1日 18時58分
-
5組織的窃盗、外国人の「トクリュウ」台頭 金属や化粧品、ファストファッションを狙う
産経ニュース / 2024年8月1日 11時14分
記事ミッション中・・・
記事にリアクションする

記事ミッション中・・・
記事にリアクションする

エラーが発生しました
ページを再読み込みして
ください
