「盛る」生産方式が脅かす地方のモノづくり/日沖 博道
INSIGHT NOW! / 2015年6月12日 9時52分
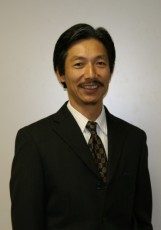
日沖博道 / パスファインダーズ株式会社
「金属積層造形」という生産革新が立ち上がろうとしている。対処のしかたを間違えると、日本のモノづくりを支える地方の金属加工業や中小部品製造業にとって致命的な事態となりかねない。
昨年、ある自治体の依頼に応じて、その地域の有力企業数社の経営課題をヒアリングしたことがあります。その1社は金属加工が専門で、日本でも数少ない複雑な加工技術が可能ならしめる、特殊な形状の掘削機用刃物加工で大企業との取引が伸びていました。経営者は非常に元気な方で、将来の展望を色々と語ってくれました。しかしその話を聞いた後で小生はその経営者に、新しい技術の習得と適用の検討を早めに始めるよう薦めました。また3年ほど前ですが、小生がMOT(Management of Technology=技術経営)の講座を持っていた大学院のクラスに金型大手の1社から学びに来ている社会人学生の方がいました。講座の合間に色々と話をしていたのですが、当時その会社の関心は圧倒的に、中国の競合が金型技術を向上させていることでした。しかし小生が注意喚起したのは、むしろ欧米での新しい代替技術でした。いずれも当事者がどれほど真剣に小生の話を受け止めてくれたかは別として、ここまでお話するだけで一部の業界の方々はピンとくるでしょう。今、欧米の製造業で静かに進行している生産革新の一つ、「金属積層造形」と呼ばれる技術です。英語でadditive manufacturing(AM:以下、「AM方式」と呼びます)、人によっては「盛る」生産方式とか「金属3Dプリンター」技術などとも呼びます。一般の3Dプリンターは樹脂素材を「盛る」だけなので、どうしてもおもちゃっぽいイメージが強いですが、金属3Dプリンターは樹脂ではなく金属粉を射出成形またはレーザー溶解することで、しっかりした金属部品や製品を成形できるのです。当然、設計データは3D-CADで作成されたデジタルデータですから、素材や製造・使用環境を考慮した加工条件を編集・修正することも手軽にできます。AM方式による最大メリットは、従来の製造法でできなかった構造の金属製品を直接作りだすことができる点です。例えば中空構造やスポンジ状の製品を一体成形できるので、素材の強度次第では非常に軽量化できるのです。または新たな機能や特徴を持たせることも可能です。先に挙げた掘削機の刃型も、ドリルやレーザーが外側から直接当たる範囲しか加工できないため形状の複雑さに限界があるのですが、金属を「盛る」方式であればほぼ限界はありません。または、従来なら別々の部品を比較的単純な形の金型で成形して、後で組みつけたり溶接したりしているので、手間が掛かる分だけコスト高になったり、経年変化で接続部分が脆くなり故障の原因になったりします。AM方式であれば最初から一体成形できるので、こうした問題は回避できます。設計データさえ切り替えれば「段取り」完了するので、多品種少量生産に向いています。こんなにいいことばかりなら生産方式が一気に切り替わりそうなものですが、そうなっていないのには理由があります。そう、この方式にもデメリットが幾つかあります。3Dプリンターの成形過程を見たことがある人ならすぐ気づくでしょうが、製造スピードが格段に遅いことがまず挙げられるでしょう。いくら一挙に完成できるといっても、従来方式で製造した部品を組み合わせるほうが圧倒的に量産に向いています。しかし生まれたばかりの技術ですので、今後のスピードアップの余地は大きいでしょう。ある程度のスピードまでくれば、あとは3Dプリンターの数を増やして、並行して同じ製品を作ることで従来方式に対抗できるかも知れません。もしくは初期量産分は従来方式のままで生産し、サービス用部品と追加生産分の完成品は在庫せずに、追加受注に応じてAM方式で生産するやり方に切り替えるところも出てくるでしょう。とはいえ、1台当りの装置コストが今のところ1億円前後と随分高いので、そうなるまでには時間がかかりそうです。しかし数年前には単純な機能の製品でさえ1千万円超だった樹脂用3Dプリンターが、今では汎用機だと100万円台で入手でき、普及機だと10万円を切るものまで登場しているほどに一挙に低価格化が進んだことを考えると、金属用でも今後予想を超えるスピードで価格低下が進む可能性は高いでしょう。AM方式で製造できるサイズがまだまだ小さいのも事実です。ただしこれは3Dプリンターのサイズが大きくなれば対処できる話です。事実、GE傘下のGE Aviationではadditive manufacturing方式でジェットエンジン(でかいことは分かりますよね)用のパーツを製作し始めています。http://www.ge.com/stories/advanced-manufacturing結局、何といっても従来と全く違う方式なので、本来の効果を引き出すべく本腰を入れて切り替えるとなると、設計~部品製造~部品調達~組立というサプライチェーン全般を見直さなければなりません。それだけ手間とコストを掛けてもメリットが上回るのかを見極めなくてはなりません。この大変さが一番大きなハードルです。したがって自動車メーカーや大型機械メーカーなど、産業構造の大本がその気になって号令を掛けない限り、なかなか切り替わらないというのが日本の現実でしょう。事実、2013 年に世界で 348 台売れている欧州製の金属3Dプリンターが、日本では2013年時点で販売実績ゼロでした(2014年11月時点でも数台と聞いています)。http://www.jetro.go.jp/ext_images/jfile/report/070...しかし欧州や米国では、完成機メーカーも部品メーカーも思い切って金属3Dプリンターを試行導入し、そして生産方式の一部切り替えが進んでいます。欧州および米国の製造業が、こうした今はまだ高価な金属3Dプリンターを購入してまでAM方式の導入を急ぐ理由は何でしょうか。もちろん、先に挙げたような、AM方式でないとできない構造の製品を製造したいというケースもあったでしょうが、実際にはそこまで設計検討を尽くして、しかも取引先との契約ができている状態になってから導入したという話は滅多に聞きません。2~3年前の技術展示会やセミナーでのコメントでは、むしろ「これは未来を決めるテクノロジーだ」「多品種少量生産へのトレンドは変わらない」「どんな新たな機能を追加できるか、これから検討したい」といった声が多かった印象があります。綿密に費用対効果を計算して踏み切ったというより、技術発展の方向性に賭けたのです。先行導入してノウハウを身に着けて、中国などの新興国とのグローバル競争に勝ちたい、といった戦略的思惑が強かったのだと小生は考えています。特に先行した欧州の製造業は、悪く云えば「バスに乗り遅れるな」、よく云えば「リスクを取らないと成功の芽を失う」といった感覚だったのではないでしょうか。それが、2013年にGEが、AM方式で先行していたイタリアの航空エンジン部品メーカーAvioを43億ドルで買収してからは、「やっぱりこの方向は間違っていない」という確信に替わったようです。今ではドイツのIndustry 4.0戦略の中核テーマの一つにまで格上げされています。http://www.plattform-i40.de/sites/default/files/Re...では今後、世界の金属加工の生産方式は一挙にAM方式に切り替わるのでしょうか。小生はそうは思いません。むしろ棲み分けが進むと見ています。事実、先行導入した欧州や米国の金属部品製造業でも、全面切り替えの前触れというより、従来方式のほうが向いている領域と、AM方式のほうが望ましい領域を見極めて展開しているようです。先に触れたGEでは、新潟県刈羽郡にあった操業62年のバルブメーカーを2011年に買収して、今ではGE オイル&ガスの刈羽事業所としてAM方式による生産を立ち上げようとしています(その試行錯誤の様子が先日のNHK総合「NEXT 未来のために」で放送されていました)が、課題も色々と明確になっているようです。http://www.nhk-ondemand.jp/goods/G2015062719SC000/例えば現時点の3Dプリンターで製造できる寸法精度は0.1ミリ程度に留まりますが、顧客の要望に応えるためにはその10倍、100倍の加工精度が必要とされます。逆に熟練の職人ならば、3Dプリンティング後の熱処理による膨張を予想して製造時の値をあらかじめ微調整することも可能だそうです。こうした実用的なノウハウが貯まることで、先行してAM方式を導入したGEなどは最適な生産方式を組み合わせて、顧客要望により的確に応えていく体制が出来上がるというわけです。言い換えれば、「そんな海のものとも山のものとも分からない技術なんぞ糞食らえ」とずっと拒否している日本の大手メーカーたちは、知らない間に世界の趨勢から大きく取り残されようとしているのです。そしてある時(かなり痛い目に遭ってから)、彼らもAM方式の意義と性能向上に気づき、急遽かつやみくもに生産体制を切り替えようとするでしょう。その際、彼らは地方の下請け加工メーカーの生産方式の転換(または追加)まで指導してくれるでしょうか。地域の金融機関は、まだまだ高価な金属3Dプリンターの導入に便宜を図ってくれるでしょうか。過去の超円高の際の行動を見る限り、そうした思慮深い行動をしてくれる大手メーカーや金融機関はごく一部に過ぎないと考えざるを得ません。きっと大半の大手完成品メーカーは単純に、自らの設計内容を変え、その3D-CADデータで生産してくれる大手Tier-1部品メーカーに生産委託するでしょう。そしてそのTier-1(もしくはTier-2の)部品メーカーはモジュール部品をAM方式で一体成形するだけで、下請けに出す度合は一挙に減る可能性が高いと推察されます。もしかすると一部の大手完成品メーカーは、自ら3Dプリンターを導入して内製化する方向に走るかも知れません。外に発注するのは、従来方式で生産するほうが有利な部品だけにするのです。そうした動きが急に始まる場合、先に触れたAM方式の、精度に関する課題等を克服する時間的余裕がなく、品質問題が急増することも予想されます。思慮のないメーカーだと、(新方式のノウハウが貯まるまで)従来方式に一旦戻すことを宣言するなど、かなりの混乱が生じかねません。いずれにせよAM方式へのシフトが本格化すると(その割合は誰にも分かりません)、今までの方式に磨きに磨きを掛けてきながら大手メーカーの海外生産シフトに苦しんできた地方の下請け部品メーカーは、さらに生産額を減らすことになりかねません。地場の金属加工業者の中には死活問題となるところも出てくるでしょう。だからこそ地方の中小加工メーカーの関係者や、地場の金属加工業を支援する商工会議所や金融機関の方々には、このAM方式に関する動きに目を光らせておいて欲しいのです。できれば皆がドタバタと動く前に、先見性のある加工業者に薦めて、(GEの刈羽事業所のように)金属用3Dプリンターを先行導入させてノウハウを貯めるように促して欲しいのです。その際に必要なら、高価な金属用3Dプリンターを導入できる体力をつけるため、合併・統合も躊躇すべきではありません。 日本のモノづくりの重要な一部が急死しないようにするため、できることは幾つもあるはずです。
外部リンク
この記事に関連するニュース
-
Meltio社の3Dプリンターを取扱う3DPCが大阪の展示会「2024国際ウェルディングショー」「第11回 METAL JAPAN」に出展
PR TIMES / 2024年4月17日 17時45分
-
高精度ロールフォーミングマシン、JIS規格鋼材、素形材(スチール、ステンレス、アルミ、樹脂)をリーズナブルな価格での提供
PR TIMES / 2024年4月14日 22時40分
-
金属アディティブマニュファクチャリング装置「Lasermeister LM300A」および3Dスキャナー「Lasermeister SB100」を発売
Digital PR Platform / 2024年4月9日 13時6分
-
製造業向け金属3Dプリンター EOS M 290 1kWの販売を開始
PR TIMES / 2024年4月5日 16時40分
-
いまだに「紙の図面」を使う製造企業が54.3%もいる…日本が「モノづくり大国」から凋落した残念すぎる理由
プレジデントオンライン / 2024年4月1日 8時15分
ランキング
-
1なぜ歯磨き粉はミント味? ヒット商品の誕生には「無駄」が必要なワケ
ITmedia ビジネスオンライン / 2024年4月26日 8時0分
-
2突然現場に現れて「良案」を言い出す上司の弊害 「気になったら即座に直したい」欲求への抗い方
東洋経済オンライン / 2024年4月26日 8時0分
-
3濃口醤油と淡口醤油、塩分が高いのはどっち?…醤油の「色の濃さ」と「味の濃さ」の知られざる関係
プレジデントオンライン / 2024年4月26日 8時15分
-
4「加賀屋」50歳の元若女将が選んだ"第2の人生" 震災からの復興への道、仕事術について聞く
東洋経済オンライン / 2024年4月26日 12時0分
-
5円安、物価上昇通じて賃金に波及するリスクに警戒感=植田日銀総裁
ロイター / 2024年4月26日 18時5分
記事ミッション中・・・
記事にリアクションする

記事ミッション中・・・
記事にリアクションする

エラーが発生しました
ページを再読み込みして
ください
